The EPS hot melting machine is also called a polystyrene/styrofoam densifier machine, a kind of plastic recycling machine. The densifier machine is used for processing and recycling EPS, and EPE waste materials, such as styrofoam fast food boxes, polystyrene packing peanuts, cake boxes, foam packaging boxes, insulation materials, and other foam materials. The foam crushing part can crush the waste EPS or EPE foam into small pieces. The melting part can dissolve the waste foam after crushing, and plasticize the foam with a screw to form a lump shape. The final foam lumps are convenient for storage, transportation, pelletizing, and sales.
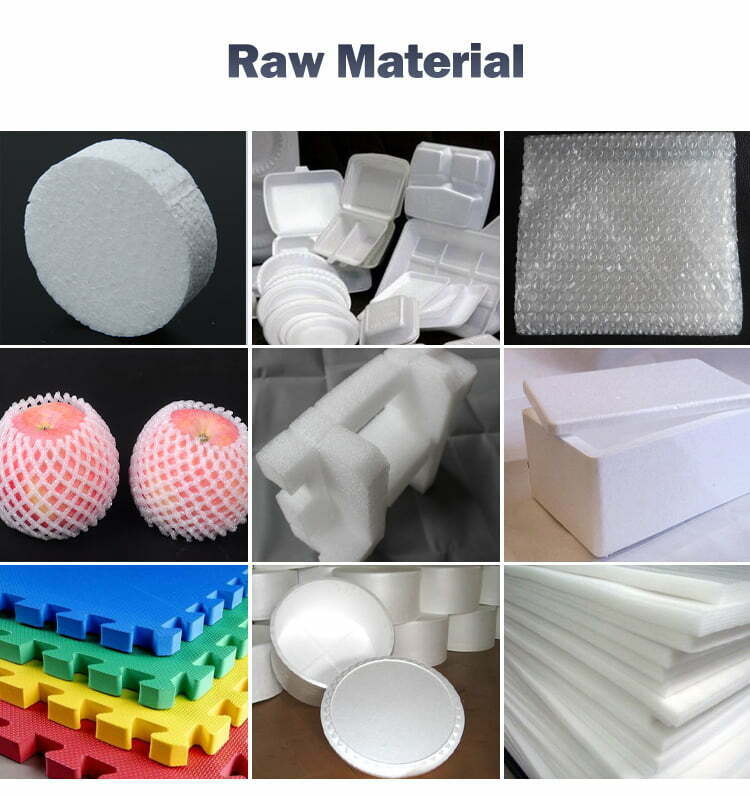
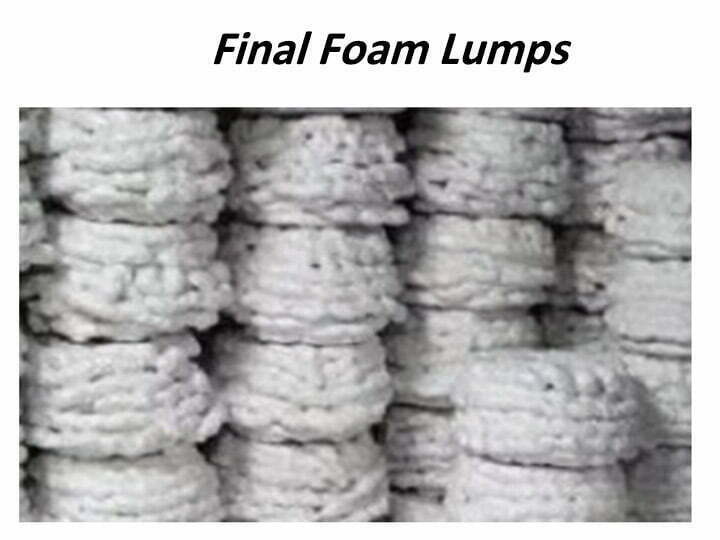
Advantages of EPS hot melting machine
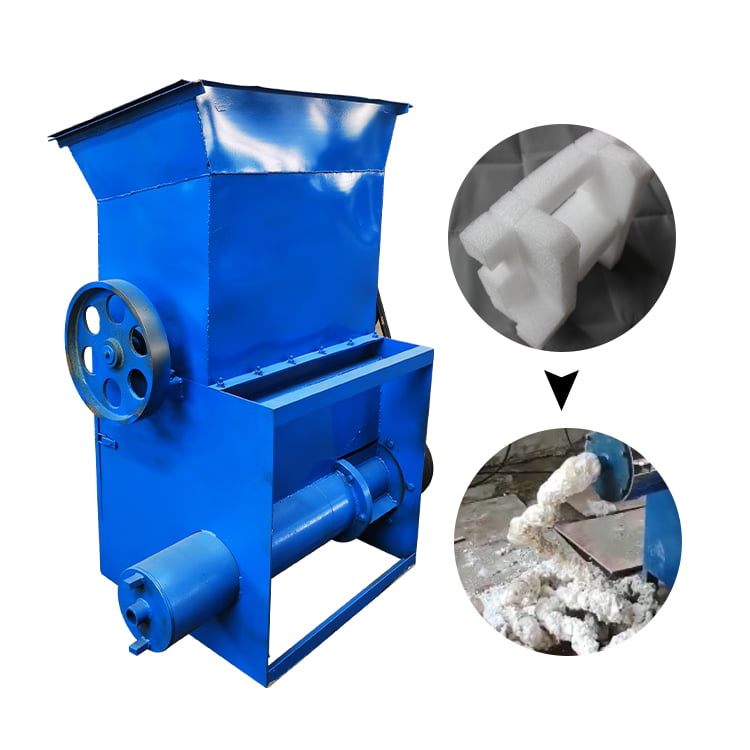
- The integral EPS foam hot melting recycling machine is a combination of crushing and foam melting. The EPS densifier occupies a small area, saves labor, and is easy to operate.
- The processing capacity of the EPS Foam Melting Machine is high, and multiple outputs can be selected. According to the different densities of foam, the output is generally about 150-250kg/h per hour.
- The power of this equipment is about 18.5-22.5kw, and the overall power cost is low.
- The final melted products take small space, which is easy for storage, transportation, and recycling.
- The automatic temperate control function can avoid abnormal situations, reaching the expected melting effect.
- Low noise, low dust, and no pollution.
EPS hot melter structure & working principle
The main part of the EPS hot melting machine is an extruder. It is made up of an extrusion system, transmission system, and heating system. The extrusion system includes the screw, cylinder, hopper, and die.
The EPS/EPE foam is plasticized into the uniform melt through an extrusion system and is extruded continuously by a screw in this process.
- Introduction of the Screw: As the main component of the extruder, it is directly related to the application scope and productivity of the extruder. It is made of high-strength corrosion-resistant alloy steel.
- Barrel: it is a metal cylinder, which is generally made of heat-resistant, high compressive strength, wear-resistant, and corrosion-resistant steel pipes. The barrel cooperates with the screw to realize the crushing, softening, melting, plasticization, exhaust, and compaction of plastics, and continuously and evenly transport the rubber to the forming system. The plasticized foam can be fully heated and plasticized.
- Hopper: the bottom of the hopper is equipped with a cutting device to adjust and cut off the material flow. The side of the hopper is a sight hole and a calibrated metering device.
Styrofoam densifier parameter (SL-800/SL-1000)
EPS hot melting densifer mode | SL-800 | SL-1000 |
Machine size | 1580*1300*850mm | 1900*1580*900mm |
Inlet size | 800*600mm | 1000*700mm |
Motor power | 18.5kw | 22kw |
Output | 150-200kg/h | 200-250kg/h |