Plastic pellet recycling machine is widely applied to various waste plastic recycling, including PP, PE plastic recycling line, and PET bottle recycling line. It can effectively recycle plastic products, convenient to store, sell, and convey, protecting the environment. Maintaining machines at regular intervals is beneficial for the service lives of the machines. The user can set up a certain time according to the production output, and runtime. Generally, regular maintenance is carried out twice a year (or running time accumulating 3000 hours) and can be conducted during production gaps or holidays. The following are the tip about maintenance on plastic pellet recycling machine.
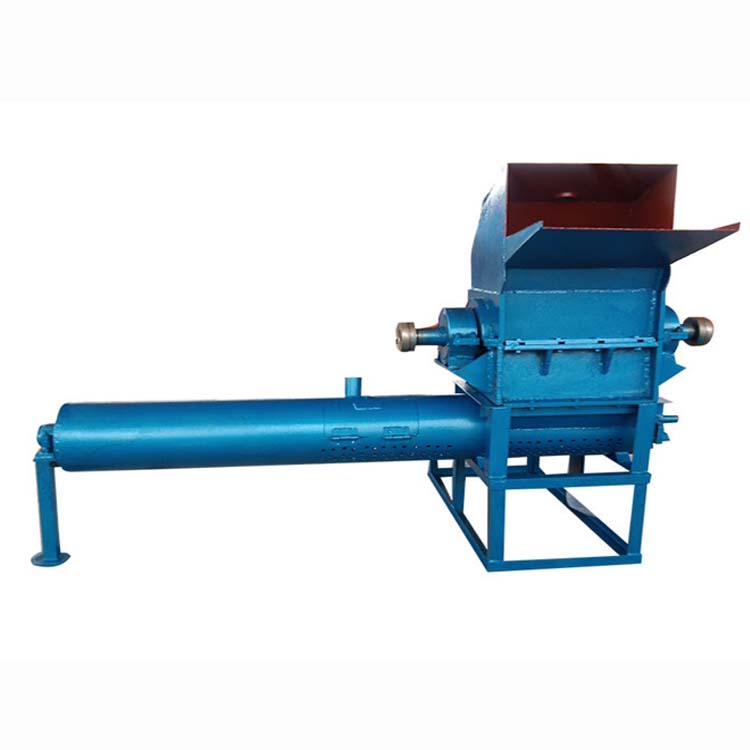
Some tips about maintenance on plastic pellet recycling machine
- Clean and wipe the dust and oil stains on all parts of the production line, tightening the loose bolts.
- Check gearbox and whether noise or not. Open the gearbox, water pump, vacuum pump, then clean the moving parts, machine body, bearing carefully. Change the lubricating oil, oil filter, cleaning oil. Check the worn condition of the moving parts, like gear, sprocket, belt pulley, water pump, vacuum pump, etc., and replacing the severely worn parts.
- Check the pressure, and the instruments of vacuum, current, voltage, heating element current; unblock the cooling water system of the feeding hopper seat; clean the cooling air duct of the cylinder; replace the compressed air and vacuum hose.
- Open the motor, check the wear of the brush, and replace the worn ones; check the wear of the rotor, send it to a professional repair shop for repair if it is obvious. Clean the motor bearings, and replace the severely worn bearings. After maintenance, install the motor, turn it on and run, check whether the spark of the motor is normal, there is excessive vibration, or not.
- Remove and clean the screw, cylinder, and head; measure the outer diameter of the screw; check whether the inner wall of the cylinder and the mold are worn and sc Partial scratches and burrs on the working surface are polished to be smooth no hanging material. When the mold surface is coated with a thin layer of silicone oil, the mold surface is eventually coated with a thin layer of lubricants.
- Use compressed air or vacuum cleaner to clean the control cabinet; tighten the loose cable and wire joints; check the cable insulation; deal with the problem immediately when discovering it; replace sheath hoses for cables and wires. Keep a record of maintenance especially for repaired or replaced parts.
- After the plastic shredder is put into use, If production stops for a short time, then carefully clean the inner wall of the pot and the blade; smear or brush lubricating oil on the main shaft bearing.
- Sharpening should be carried out after one month of moving knife work. If necessary, sharpening can be carried out at any time according to the situation. For plastic shredder, you need sharpen it when the dealt materials reach about 10000kg.
- Maintenance of the whole machine after six months of operation (8 hours per day)
- Keep the plastic pelletizer in good condition and clean up the dust and scattered pellets of the granulator in time; check the operating situation of the plastic pelletizer at any time, paying attention to whether there is abnormal noise or blockage of the pelletizing chamber.
- Remove the agglomerates in the strips in time to prevent large blocks from entering the plastic pelletizer; strictly prevent metal and other items into the plastic granulator.
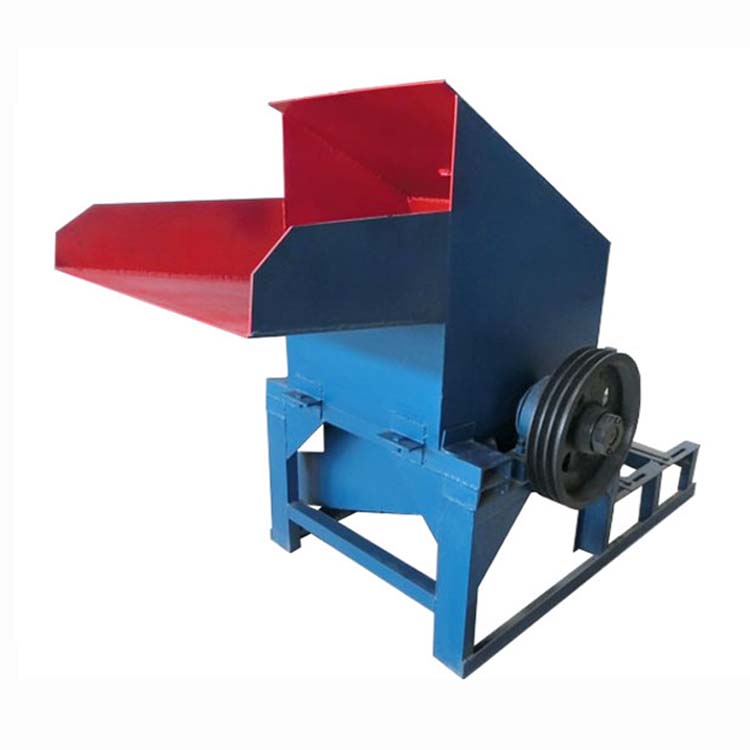
Conclusion
No matter how good machines are, maintenance is an extremely important factor for its service life. Terrible using method and ignoring maintaining process is not beneficial for machine running. What’s more, it may be a potential safety risk. Therefore, paying attention to maintenance and right operation is good for your machines and yourselves.