Plastic granulator machine also called plastic granules making machine. It is the equipment to melt extrude waste PP(polyethylene) or PE(polypropylene) chips so as to make plastic granules. The main engine of the granulator is an extruder, which consists of an extrusion system, a transmission system, and a heating and cooling system. Broken, cleaned, and dried plastic can be directly put into the extruding machine. Then the extruded plastic strips usually need to be cooled in a cooling tank and cut into pellets by a pellet cutting machine. The plastic film pelletizing machine is an important part of the plastic recycling plant. It’s beneficial for vigorously developing renewable resources and turning waste into treasure.
Working video
Applicable material for recycling granulator
The design of the plastic granles making machine allows it to efficiently process a wide range of waste materials into pellets. For waste plastics we divide them into post-consumer and post-industrial plastics, both of which can be processed in our recycling machines.
Post-industrial recycling materials: In order to save on raw material costs and to realize a circular economy, many plastics producers like plastic bag manufacturers recycle their trimmings and then continue to process the pellets they produce into plastic products. These post-industrial plastics include HDPE/LDPE bag cut-offs, film-on-rolls, defective film and bag products, printed zipper bags, defective HDPE PVC pipes, PP/HDPE/LDPE regrinds, HDPE soft/rigid irrigation pips, etc.
Post-consumer recycling materials: All used and discarded plastic products such as used plastic bottles, plastic bags, abandoned meters, car parts, food containers, chemical drums, plastic pallets, PP ropes, plastic lumps, jerry cans, cosmetic tubes, bubble wraps, laminated/multi-layer films, flexible packing materials and so on.
Plastic granulator machine for sale
As the main machine of the plastic granule production line, the equipment applies to a variety of materials pelletizing. The appearance of the granulators for handling different materials are similar, but not the same. Their internal components need to be adjusted according to the specific material, such as the diameter of the internal screw, the distance between the screw and the barrel wall, and the length of the screw.
Therefore, one adjusted machine corresponds to one kind of material. The adjusted equipment is more suitable for the property of your raw material. So you can get in touch with us to get more detailed information by telling us what material you want to pelletize. Besides, we support customization services according to your specific recycling requirements.
Factory machine display scene
Features & benefits of plastic granulation equipment
- Unique design, good performance, low noise, stable running, simple operation
- Simple process, advanced technology, and suitable for various waste plastics
- The screw and barrel are wear resistance, durable, high output.
- The plastic granulator machine can deal with 2-30 tons of waste plastic per day.
- Integrated main and auxiliary machines, simple installation, small footprint, high-cost performance.
- Use high-pressure friction uninterrupted heating, multi-function heating mode, equipped with a constant temperature system
- Do not need to heat continuously, reducing energy consumption by 30-40%.
- High automation, a few human interventions
- Customization service is available.
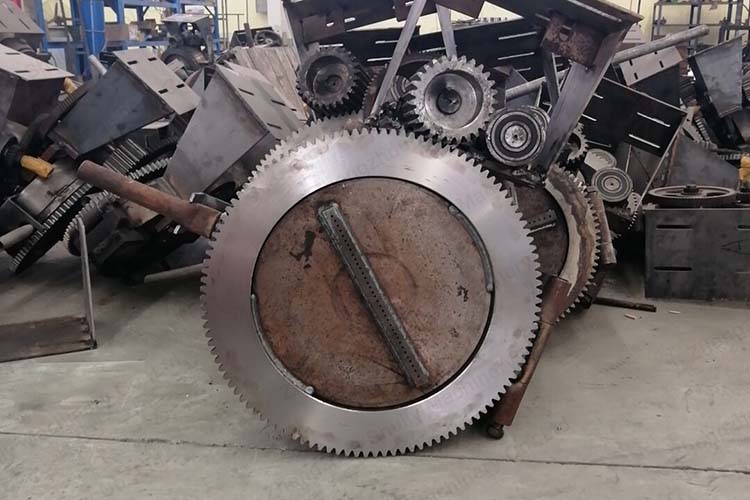
Structure of the machine
The plastic granules making machine structure is composed of a reducer, feeding port, heating device, press chamber, discharge port, screw press, mold head, base, and other parts.
The reducer is a hard gear surface reducer. Its quality is greatly important as a crucial part of the plastic extruder. At present, the quality ranking of common reducers on the market is old-style snail reducer <common reducer <semi-hard gear surface reducer <hard gear surface reducer.
There are main two types of mold head for plastic extruding, electric die head, and hydraulic die head. The filer screen of the hydraulic mold head can be replaced without stopping the machine. For the material with many impurities, the hydraulic one is more suitable. But the cost is also higher. The model of the plastic granulator machine is mainly divided by the diameter of the screw. The screw is made of 45#steel, 40CR, 38CRSI. The model of the plastic granulation equipment is mainly divided according to the diameter of the screw press. Customization services of chrome plating, nitriding, and other processes are available according to their plastic processing characteristics.
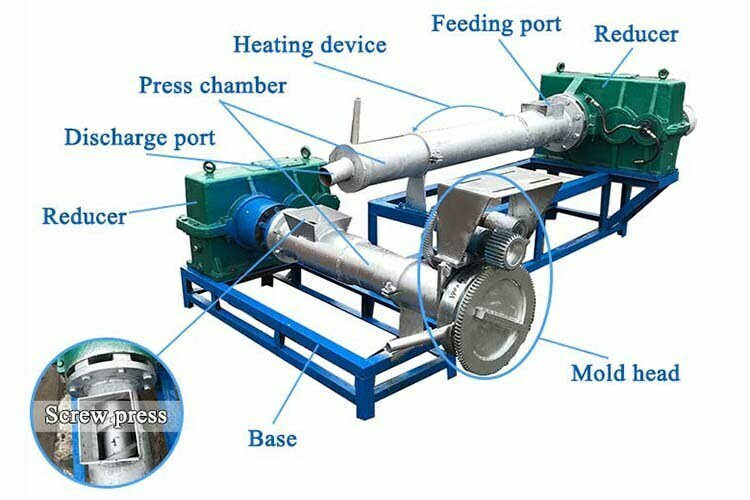
The heating system of the LDPE/HDPE granulating machine
The heating method of the plastic extruder is divided into a cast aluminum heating ring, quartz tube heating ring, ceramic heating ring, electromagnetic heating ring. Among them, the best heating effect is electromagnetic heating. The cast aluminum heating ring needs 30-40minutes for heating, while the electromagnetic heating ring needs 15-20 minutes. Electromagnetic heating can increase the temperature quickly. And it has a good constant temperature effect, running stably. But it is not suitable for processing foam materials. The heating method should be considered based on the raw materials and the color of the final product.
Working principle of the plastic granule making machine
- Turn on the HDPE/PP/PVC granulaing machine. Looking at the machine whether there is abnormal sound or vibration. If not, put it into use.
- Pay attention to preheating the plastic granulator machine so as to melt the plastic. The melted plastic will turn black if the temperature is too high. While low temperature can not melt the plastic.
- It’s better to be equipped with an automatic feeding machine to feed plastic chips into the plastic granulation equipment because the plastic film material is very light, uneasy to feed.
- The plastic film chips will be melted and pressed into the main engine, then pushed along with the screw into the auxiliary engine. Finally, The melted material will be extruded from the auxiliary engine in the form of plastic strips.
- Place a cooling tank under the mold head so that the hot plastic strips cool in the tank and shape.
What should pay attention to when using plastic granulator equipment?
- The inside of the machine should be no metal residue or fine sand. Do not place metal objects or other things around the inlet where may fall into the machine in case damage to the plastic pellet machine, cause jamming, or destruction.
- The operator had better receive actual training about how to operate the granulating machine. In addition, they should also learn the structure of the equipment and operating procedures.
- Control the water temperature of the cooling tank. Because the plastic strips will be broken if the temperature is too low. While high temperatures can not make plastic strips cool and shape well, and the strips may stick.
- The melted plastic should be extruded into strips evenly before entering the plastic pellet cutting machine. Uneven strips may damage the plastic pellet cuter. The holes of the mold head may be clogged with impurities if the extruded strip is thin or broken. So you need to replace the filter screen.
Parameters of HDPE granules making machine
Type | 105 | 125 | 135 | 150 | 180 | 200 | 220 |
Screw diameter | 105mm | 125mm | 135mm | 150mm | 180mm | 200mm | 220mm |
Spindle speed | 50-70/min | 50-70/min | 40-50/min | 40-50/min | 40-50/min | 40-50/min | 40-50/min |
Main motor power | 18.5kw | 30kw | 37kw | 37kw | 55kw | 75kw | 90kw |
Reducer (hard gear) | 200 | 225 | 250 | 250 | 280 | 315 | 330 |
Weight | 1.3T | 1.8T | 2T | 2T | 2.2T | 2.8T | 3.2T |
Size | 2.4*0.7*0.7 | 2.6*0.7*0.7 | 2.8*0.7*0.7 | 3.0*0.7*0.8 | 3.2*0.7*0.8 | 3.5*1*1 | 3.8*1.2*1 |
Output | 150kg/h | 180kg/h | 200kg/h | 300kg/h | 350kg/h | 380kg/h | 420kg/h |
We have 7 models of granulator machines for you to choose from. The biggest difference between the 7 machines is the output. The output is 150kg/h, 180kg/h, 200kg/h, 300kg/h, 350kg/h, 380kg/h and 420kg/h respectively. Similarly, different output corresponds to different prices. If you have a large plastic recycling plant, we suggest you buy 380kg / h or 420kg / h machines. We will also give you the best price. Secondly, you need to consider your plant area and machine size. As you can see, larger production means larger size. For example, the size of a machine with an output of 150kg/h is 2.4 * 0.7 * 0.7, while the size of a machine with an output of 420kg/h is 3.8 * 102 * 1. If your plant area is too small, it is not suitable for oversized machines, or you can adjust the size of your plant.