The extrusion cooling tank is an important part of the plastic pelletizing system. It cools and shapes the extruded molten plastic and helps to lay the foundation for subsequent plastic dana cutting. This post will explain our water baths for granulation in detail.
Why We Need The Water Cooling Bath For Plastic Pellets?
- Cooling: Waste plastics are melted and extruded at high temperatures, so they soften, deform, and even break easily and need to be cooled by extrusion cooling tanks.
- Shaping: The quality of the recycled pellets is influenced by the size, surface smoothness, and uniformity of the plastic extruded from the die head. Cooling and shaping the strips in a cooling bath can enhance the quality of the resulting pellets and prevent the plastic from sticking together at high temperatures.
- Energy-saving: Compared to other cooling methods, the water bath for plastic is more energy efficient, environmentally friendly, and reduces operating costs.
- Extend The Plastic Dana Cutting Machine’s Life: Plastic strips that have not been cooled sufficiently to enter the downstream granulator will jam the plastic pellet cutter blades, cause uneven cutting, and even damage the equipment. Cooling the plastic will help ensure smooth subsequent cutting.
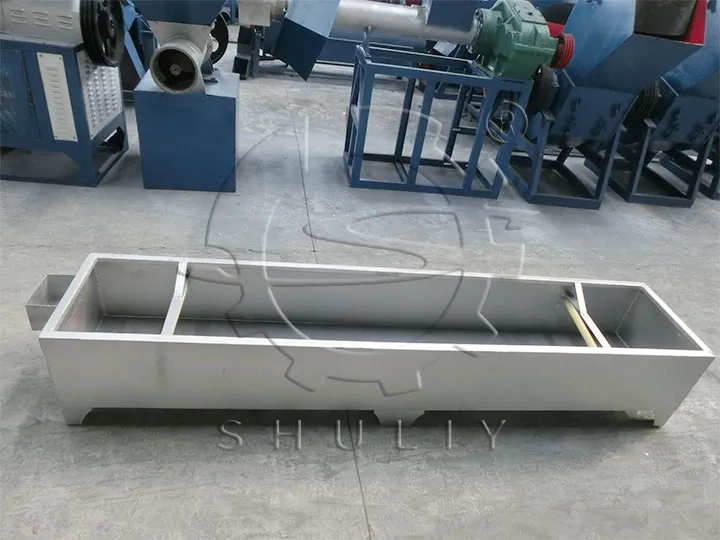
Key Features of Our Extrusion Cooling Tank
- Reasonable design of the extrusion cooling tank size so that different plastic materials can be fully cooled at the same time, but also to avoid poor material flow and wasted energy.
- Made of high-quality stainless steel, our strand cooling bath is durable, corrosion resistant, and has good thermal conductivity, which can efficiently cool the plastic strips.
- Adjustable water flow in the water bath to ensure uniform cooling of the plastic.
- Convenient docking, the cooling tank can be used in perfect cooperation with various types of plastic extruders and plastic dana cutting machines to jointly promote recycled granules manufacturing.
- Equipped with waterproof and leakproof safety sensing device, high safety.
- Easy to clean and maintain and environmentally friendly with low energy consumption.
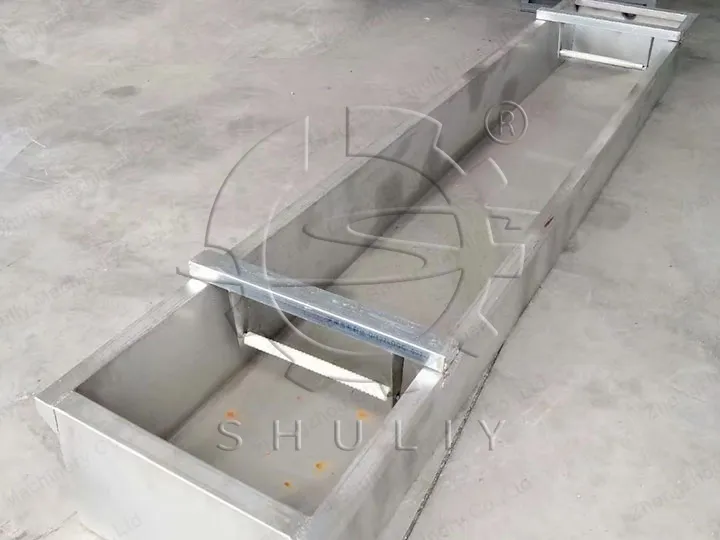
Details About The Plastic Cooling Tank
Size(m) | 2.5*0.4 |
Material | High-quality stainless steel |
Raw Material | Extruded plastic strips from the die head |
Function | Cool and shape the plastic strips |
Services | Custom, technical support, and a one-year warranty |
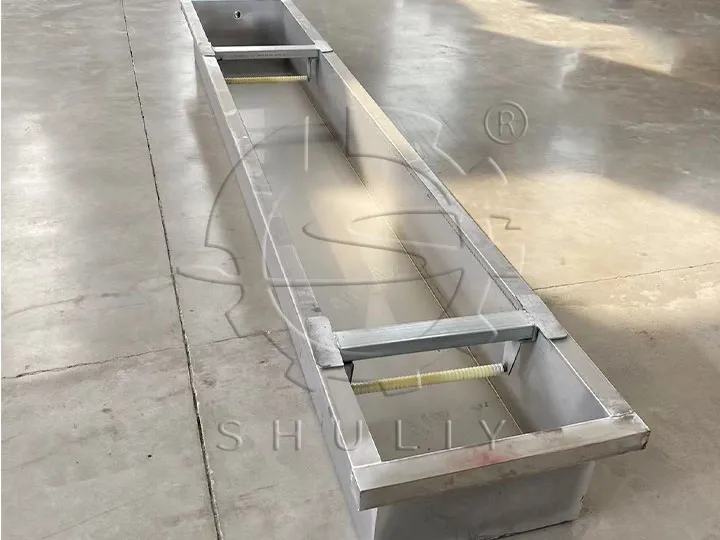
How Does The Plastic Water Bath Work?
After the plastic is extruded from the die head of the pelletizer at a high temperature, it enters the extrusion cooling tank. The water in the tank serves as the cooling medium, quickly and evenly absorbing heat. This heated water flows through a circulation system, passes through a heat exchanger, and returns to the tank to maintain a consistent cooling process. Finally, the uniformly cooled plastic is transferred to the pelletizer for cutting, facilitated by an automatic lifting device.
During this process, the temperature and flow rate of the circulating water can be adjusted using the pelletizer’s intelligent cabinet to meet the cooling requirements of different types of plastic. Additionally, the cooling water can be drained and replaced periodically to ensure optimal performance.
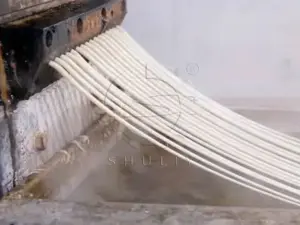
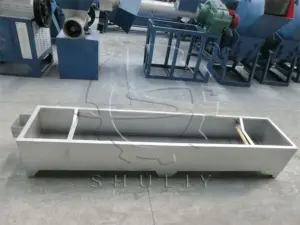
Precautions For Use
- Be sure to replace the cooling water and clean the extrusion cooling tank regularly to maintain the cleanliness of the material and to prevent contaminants from clogging the pipes or corroding the tank.
- Adjust the water flow rate and temperature to meet the different cooling needs of different materials.
Summary
As an important part of the plastic pelletizing system, a extrusion cooling tank is often used with a plastic extruder and plastic pelletizer. It helps to cool and shape the plastic extruded by the plastic extruder machine. If you want to know more about plastic pelletizing, please contact us and we will recommend the right equipment for you!
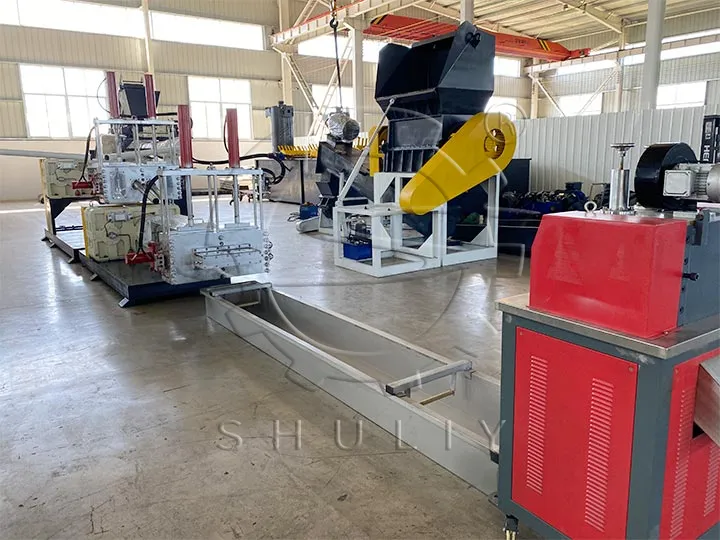